Pressure Die Casting Service
Step Rapid offers a turn-key high-pressure die-casting solution for your needs. utilizing state-of-the-art equipment to help customers realize their product designs at an economical rate. Expert pressure dies casting services with greater customization options, high rates of manufacturing, low costs, and increased strength plus corrosion resistance are just some of the benefits. Automated pressure die-casting services to ensure we optimize production for your budget even for highly specialized parts.
What Is Pressure Die Casting?
Pressure die casting is a means of mass-producing low-temperature metallic components with a high degree of precision and repeatability. Unlike gravity die casting, the process is automated and the liquid metal or alloy is injected under high force into a hardened steel tool. This means pressure die casting can be performed at a low per-unit cost in longer production runs which soon makes up for higher initial tooling costs. It’s the fastest and most cost-effective way to produce medium to high volumes of metal parts with excellent surface finish and dimensional accuracy.
Advantages
- Ability to produce high volumes of identical metal components, with high levels of accuracy
- Cost-effective solution for the mass production of castings
- Complex geometries can be achieved
- Especially suited for larger metal parts
- Can produce thousands or even millions of components before needing to be replaced.
- Ideal for a wide range of applications
- Great for highly complex and precise components
- Suited to long production runs or where large volumes are needed
- Close dimensional control and good surface finish
- Castings with thin walls, and so lighter in weight
- Most pressure diecasting’s can be discreetly electroplated without any further processing
- Works with aluminum, zinc and magnesium
- Mold tools can make tens of thousands of parts economically
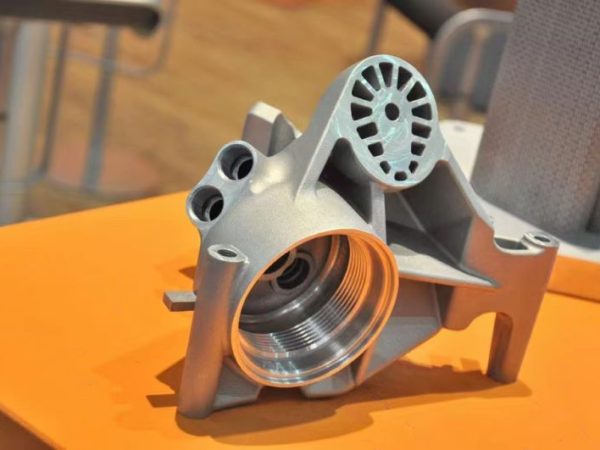
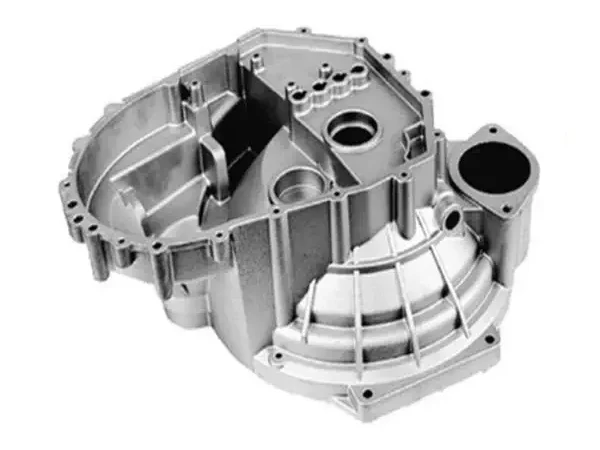
Why Choose Step Rapid for High Pressure Die Casting?
Effective Communication
You will benefit from communicating with technical sales who know bette to suport what you need and discuss more options to find out the best fit for your projects manufacturing, and know-how to guide you to the quick path and move projects ahead significantly. rest assured that you will know more about manufacturing process from the conversation we do.
Expertise And Experience
To make sure that the right party you connected to, all sales in Step Rapid are well-trained and experienced with over 100 projects and help customers to reach their final production, nothing better than the experts who can guide you in the whole project, all you need to do is to trust us and enjoy the experience we share. which benefit your products or projects.
Authentic Materials Assurance
All production and parts start from materials seletions , At Step Rapid, we can advise materials while you are not sure which type would be ideal base on product functionality. we help to idendify the best fit. And you get full material traceability so you can meet your critical product certification and licensing requirements.
Add-on Services
Most of the project can not finished by one process, We offer a full suite of add-on services to complete your project to the highest specifications. which includes CNC milling and turning, aluminum extrusion, EDM processing, a series of finish services and more.
The Pressure Die Casting Process
The success of your pressure die-casting project depends on the quality of the mold tools, and our mold-making abilities are unmatched. After we receive your order, we will:
- Preparing the mold. This important first step is key to the finished product. By applying a lubricant to the inside of the mold, the manufacturer regulates the temperature and creates a film between the mold and the molten metal that will be put inside. This allows for easy removal of the casting. After applying the lubricant, the mold is closed and sealed.
- Injection. This is the stage where the manufacturing company puts molten metal into the mold. The metal is injected at a pressure somewhere between 1,500 and 25,000 PSI. The die-casting mold then maintains this pressure until the metal has solidified.
- Ejection. This step requires the ejection of the solidified metal from the mold. This is done by releasing ejector pins that are a part of the mold.
- Shakeout. The final step of the process is where scrap metal gets separated from the newly made metal object. This is simply the process where the manufacturer cleans out the mold so it can be used again.
Tolerances
We follow strict standard tolerances for pressure die-cast parts. However, if your requirements are very precise, additional post-process machining can help you to achieve your tolerances.
Materials
Mold Tools
Our mold tools are usually made from 8407 or H13 tool steel with a Rockwell hardness of 42-48. Specialty steels are available upon request.
Production Parts
We provide high-pressure die casting in several different alloys of aluminum, zinc, and magnesium. Your choice of materials may depend on cost, weight, and performance. Here are some tips:
- Aluminum is ideal for strong, lightweight yet complex geometries. It can also be highly polished. Our alloys include ADC12, A380, ADC10 and A413.
- Zinc is the least expensive but is good for plating. Available alloys are Zinc #3 and #5.
- Magnesium offers the best strength-to-weight ratio for higher-performance applications. We offer magnesium alloy AZ91D.
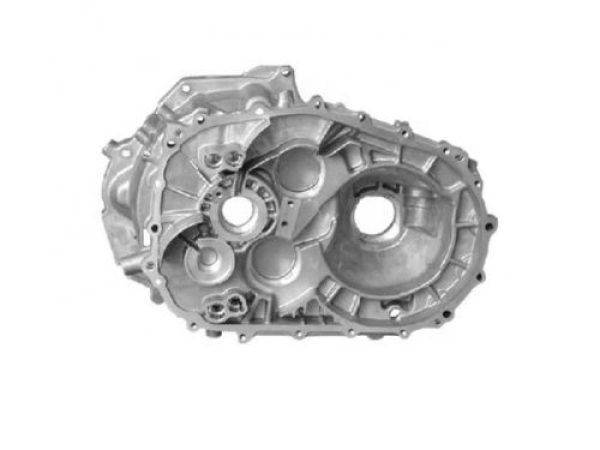
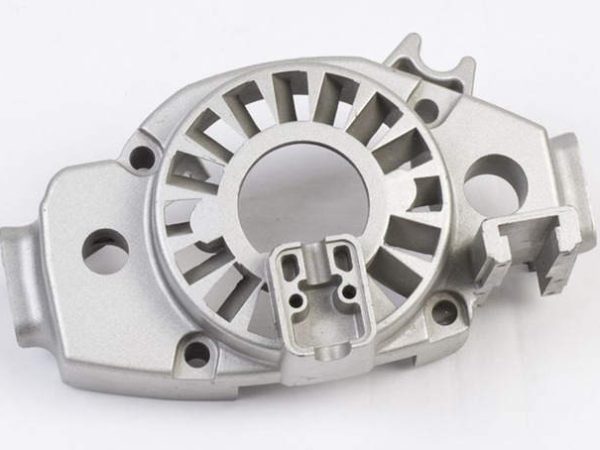
Request Your Free Pressure Die Casting Quote Today
Our engineering-dedicated team are ready to work on your next projects by delivering the best solutions. Most quotes are delivered within 24-hours, or less, depending on the project details. Sales engineers will reach out to you and build up the most effective conversation and support you continuously!